前回は、原価企画のPDCAサイクルと、それを実行していくにあたっての前提条件についてお話しました。
今回は、PDCAのD(実行)にあたる、製品の開発・設計段階で具体的にコスト低減案を出していく手法について考えていきたいと思います。
まず、コスト低減案を出していく取り掛かりとしての代表的な手法として、「全バラ検証」とか、「ティアダウン」と呼ばれる手法があります。
これは、競合他社の製品を分解・分析し、他社のコスト削減手法を自社製品の設計において参考とする手法です。
製品全部をバラバラにするので、全バラとよく言われていますが、例えば自動車メーカーのように大きな製品を扱う企業でも、他社の自動車をネジの一本単位まで分解しています。
また、他社の製品だけでなく、自社の前モデルも分解して、他社のものと比較していきます。
自動車メーカーを例に出すと、話が非常に大きくなってしまいますね。
でもこの全バラ検証は、もっと小さな製品にも当てはめられると思っています。
私が中小製造業のお手伝いをさせていただいて感じるのは、意外と競合他社の製品を(細かくは)知らないということです。
しかし、細かく見ていくと、結構参考になることも多いと思うのです。
全バラ検証にあたってのポイントは大きく2つです。
1つは、製品全体として部品点数や標準化率などを見ていきます。
例えば、部品点数が他社製品のほうが圧倒的に少ない場合は、組立にかかる工数がそれだけ違うことになります。
そこで、どのように部品点数を削減しているのか、どのような機能を廃止しているのかを、全体的に見ていきます。
もう1つのポイントは、部品毎の詳細についてですが、以前にもお話しました通り、全ての部品を1点1点比較するということではなく、コスト低減ニーズの高い主要部品について比較をしていくということです。
競合他社の製品が、安価な材料を使っていたり、造りやすい・組み立てやすい設計をしていたり、コストの安い海外でも製造ができる設計となっている場合には、こうしたノウハウを学び、自社製品の参考にします。
もちろん、そのように変更して製品の機能や精度に影響がある場合には、どこまでが許容範囲かをお客様の視点で考えていくことになります。
全バラ検証では、原価企画のプロジェクトメンバーのみならず、一定期間は展示室のようなものを作り、全従業員が参加できるようにすることがとても重要です。
前回の補足になりますが、プロジェクトメンバーといっているのは、中小企業では原価企画の専門部署を抱えることはとても困難だからです。
そこで、各必要部署からメンバーを出し合い、新製品の開発兼原価企画にあたるプロジェクトを結成することが良いと思います。
これらのメンバーは通常業務もあるため多くの時間を取れないということを考慮し、他の従業員のアイデアを活用できる仕組みづくりが必要です。
全バラの展示室にアイデアカードを設置して、全従業員からアイデアを募るなどです。
また、ゲストとして取引業者さんに入っていただくことも、効果が高まるのではないでしょうか。
良いアイデアについては、トップから表彰するなども意欲を高めるために良いかも知れません。
次回は本シリーズの最終回です。
最後に、部品毎にコスト低減を図っていくための着眼点について、もう少し詳しく見ていきたいと思います。
この記事の執筆者
犬飼 あゆみ
(株式会社みどり合同経営 取締役/中小企業診断士)
一橋大学法学部卒業、大手自動車会社のバイヤー(部品調達)として勤務後、当社へ入社。
企業評価における事業DDのスペシャリスト。事業DDでの経営課題の洗い出しをもとに、事業計画や経営計画(利益計画&行動計画)の策定・実行支援が専門分野。
この記事の執筆者
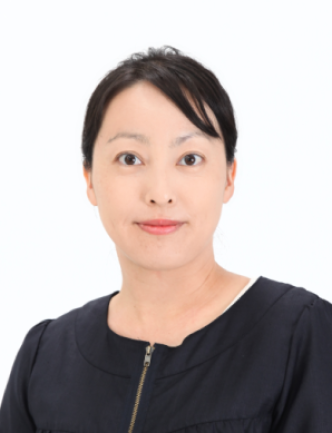
犬飼 あゆみ
(株式会社みどり合同経営
取締役
中小企業診断士)
一橋大学法学部卒業、大手自動車会社のバイヤー(部品調達)として勤務後、当社へ入社。
企業評価における事業DDのスペシャリスト。事業DDでの経営課題の洗い出しをもとに、事業計画や経営計画(利益計画&行動計画)の策定・実行支援が専門分野。